The production of side gusseted pouches is the latest intersection of material science, engineering precision, and advanced production techniques. With their expanding sides and upright feature, the pouches have made themselves a ubiquitous packaging solution within pet food, dry products, and consumer packs that require both functionality and cosmetic appeal. The intricate process of their production ensures that they meet high levels of durability, protection, and convenience, making them a vital component of modern packaging systems.
This article provides an entire analysis of the manufacturing process and technological advancements in producing side gusseted pouches. From each step—from selecting material to ensuring quality—readers will become familiar extensively with how these pouches are manufactured and why they have become essential in delivering products to customers in an efficient and assured reliability.
Understanding the Side Gusseted Pouch
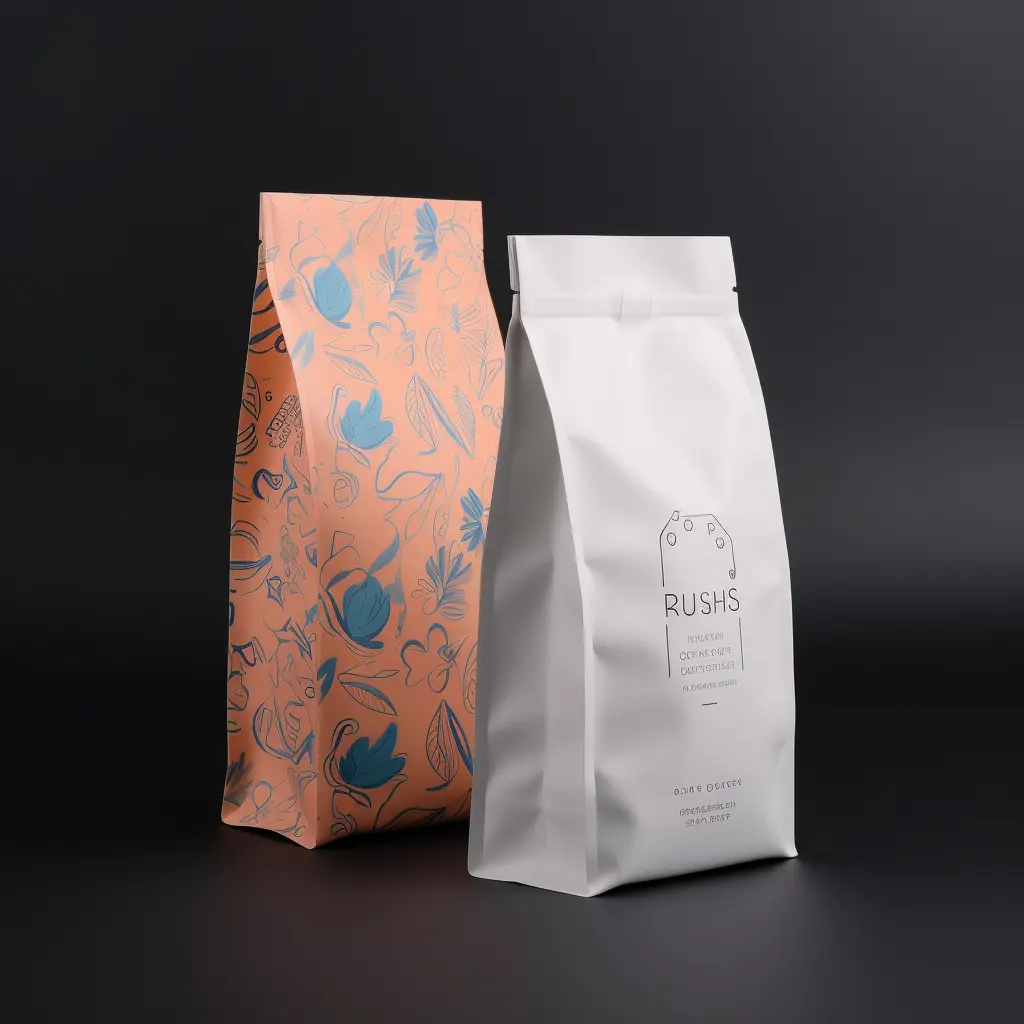
A side gusseted pouch consists of folded side panels, or gussets, that allow the pouch to stretch as it fills with contents, creating a box-like, rigid shape. This design has several advantages: it delivers the maximum amount of storage space, enables the pouch to stand on shelves, and provides considerable surface space for labeling and marking. In packaging pet food, side gusseted pouches are widely employed for dry kibble, treats, and specialty foods due to their ability to maintain product freshness and withstand handling.
There are a number of steps involved in creating a finished pouch from raw material, each requiring specialized equipment and expertise. The following addresses the key steps in the process.
Step 1: Material Selection
The foundation of any side gusseted pouch is the right selection of materials. The companies employ multi-layer films, which are produced by blending polymers and other substrates to give a blend of strength, flexibility, and barrier qualities. Some of the usual materials employed are:
- Polyethylene (PE): A flexible, water-resistant coating that protects the contents from humidity.
- Polyester (PET): A tough outer layer that gives structural strength and allows high-quality printing.
- Aluminum Foil: A reversible mid layer that shields from light, oxygen, and water, providing shelf life.
- Polypropylene (PP): A durable material often used in resealable seals or included for added heat resistance.
For packaging purposes like pet food, all the materials must be food-grade and free from toxic chemicals contamination, such as BPA, to provide safety. The rise of sustainability concerns has also made it necessary to use biodegradable alternatives like kraft paper or PLA (polylactic acid) in eco-friendly pouch designs.
Step 2: Film Lamination
Once the materials are chosen, they are laminated into a single unified film. Lamination is the bonding of layers using adhesives or heat to create a composite material that benefits from the strengths of every material. For instance, an external PET layer would be applied to the outside for strength, and an internal PE layer for a secure seal. Lamination is carried out with precision by machines like extrusion laminators or gravure presses, which guarantee uniform thickness and adhesion throughout the film.
The laminated film obtained is the raw material for pouch manufacturing, which gives the barrier properties necessary to protect contents from environmental factors such as air, light, and moisture.
Step 3: Printing and Design Application
Before shaping the film into pouches, manufacturers apply designs, logos, and product information through advanced printing techniques. Side gusseted pouches offer big surface area, which makes them ideal for detailed branding. Two major printing processes are employed:
- Rotogravure Printing: Engraved cylinders are utilized in this technique to transfer ink onto the film, yielding deep, uniform results well suited to mass production runs.
- Flexographic Printing: Lower cost and flexible plates, often chosen for simpler designs or minimal production runs.
The inks used are usually UV-stable to avoid breakage over the years, with labels—such as pet food packaging nutrition labels—still being legible through the product lifespan.
Step 4: Pouch Forming
Flat film is transformed into a three-dimensional pouch during the forming stage. VFFS equipment and other specialized machinery are used to shape the film. Several key movements are in the process:
- Gusset Folding: Folding the film over the edges to create the gussets that extend, thus giving the pouch its distinctive form.
- Bottom Sealing: Heat-sealing technology seals the bottom seam, providing a sturdy base that allows the pouch to stand upright.
- Side Shaping: Certain tools are used to ensure gussets are folded evenly, maintaining symmetry of the shape and integrity of the structure.
Additional features—like tear notches for easy opening or tracks for resealable zippers—may be incorporated at this point, depending on what use the pouch is intended to be put to.
Step 5: Filling and Final Sealing
When the pouch is formed, it moves into the filling stage, where the product—pet food kibble or treats, say—is filled automatically into the open top. High precision in filling is needed to have the same weight and volume every time, thus avoiding loss or customer dissatisfaction.
Upon filling, the top of the pouch is heat-sealed or ultrasonically sealed with a tight closure that keeps foods fresh. Within repeated-use pouches, the seal has resealable closures like sliders or zippers to make things more convenient to end-users.
Step 6: Quality Assurance
A necessary final step for quality assurance ensures that pouches meet industry requirements. Detailed testing includes:
- Seal Strength: Pressure tests to verify that seals remain leak-proof during use.
- Barrier Effectiveness: Test for moisture and oxygen barrier resistance.
- Durability: Drop testing and compression test mimics actual usage conditions to guarantee the pouch strength.
In packaging pet food, compliance with regulations—e.g., FDA or AAFCO—is necessary to provide safety for both animals and human beings.
Technological Innovations in Manufacturing
The production of side gusseted pouches has been optimized through technological innovation, improving quality and efficiency:
- Automation: Conveyor belts and automation reduce repetitive movements, reducing defects and increasing capacity.
- Smart Monitoring: Sensors in machines monitor irregularities during sealing, printing, or lamination, ensuring consistency.
- Environmentally Friendly Process: Biodegradable film can be processed by new technology, enabling a shift toward environmentally friendly package solutions.
These advancements enable the manufacture of pouches that not only work effectively but also fulfill the evolving needs of the market.
Applications and Benefits
The method of manufacturing side gusseted pouches is designed to create a product with special advantages. Their vertical standing enhances shelf visibility, while gusseted construction allows them to utilize storage space optimally. In pet food packaging, the multi-layered design ensures long-term freshness for kibble by preventing moisture and oxidation. Other features like resealable closure are also targeted towards convenience for consumers, which makes them a perfect choice for households.
Conclusion: Precision in Packaging
The manufacture of side gusseted pouches is a testament to the precision and ingenuity of modern manufacturing. From the selection of high-performance materials to the incorporation of advanced sealing technologies, each step leads to a packaging solution that is all about form, functionality, and reliability. For uses like pet food, where safety and freshness are the ultimate goals, these pouches offer an ideal combination of convenience and performance.
The admiration of this process is a testament to the nuance behind as simple-seeming a package, revealing the craftsmanship that keeps products out of consumers’ hands in the optimal manner. As the future progresses and technology continues to evolve, side gusseted pouches are well on their way to commanding packaging innovation again, serving businesses and customers alike.